Optical Fiber Curing 101: From Epoxi to UV.
Optical Fiber Curing 101: From Epoxi to UV.
The optic fiber cables need to be protected with coating materials like acrylate polymer or polyimide and cured either with UV light or heat used in a specific oven made to cure the optic fiber cables.
Acrylate polymers are applied in most cases in a two layer coating system, with a softer inner layer called the primary coating and a harder outer layer called the secondary coating, this can be made for reduced micro-bending loss. The temperature rating for typical acrylates is 80°C and the higher temperature acrylates are for 150°C.
Polyimide polymers is a non-acrylate specialty fiber coating material that is used for harsh environments, or serving as a secondary cladding. Fibers that are coated with this material has the widest temperature range that goes from -65°C to 300°C or even 400°C.

These polymers offers mechanical and chemical protection from the environment, having each of them characteristics that provides properties for optical fiber to meet customer requirements.
The most used ways to cure an optic fiber cable are by UV and Heat oven, the UV can be UV arc lamp or microwave excited UV lamp, these systems are used to cure the fiber coatings.
Some of the advantages of curing an optic fiber with UV are the following:
- High and better production speeds.
- Reduced downtime.
- UV technology allows the curing process to be done faster and more efficiently with less waste.
- Higher quality and more durable optical fibers and cables.
- More durable marking identification on wires and cable jacketing.
Regarding the disadvantages the followings are the most significant:
- Low efficiency. UV lamps are inherently inefficient in producing UV light, which results in higher electrical operating costs.
- Ballast replacement. The ballast in the power supply of UV microwave systems must be frequently replaced. This results in manufacturing downtime and additional cost in terms of parts and technical support.
Heat curing oven, this is another method used for curing the fiber cables connectors such as FC, SC, LC, MU, MTRJ, ST, MPO etc. Also depending on the manufacturer it comes in different sizes and with different capacities to cure 20, 50 or more cables at one time, this type of curing can use a highly precision temperature control system that is adjustable from 0° to 160°C, this oven has the advantage that can be used indoor or in the field.
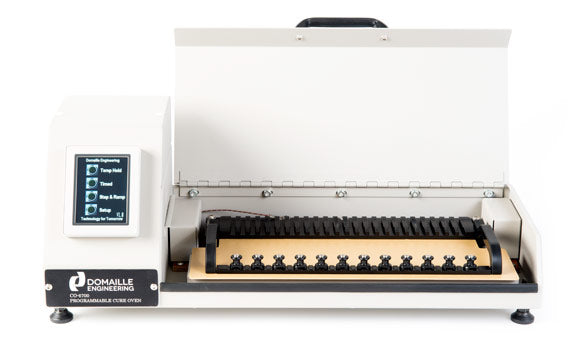
Source and example of Heat Oven: Domaille Engineering
Some of the advantages of curing an optic fiber with a heat over are the following:
- It is simple and viable.
- It can be small and easy to carry.
- The curing tools can easily be replaced.
Regarding the disadvantages the followings are the most significant:
- The connector must be cured in an electric oven, this one should not be used in environments where there is combustible fumes.
- A fiber optic connector heat oven cannot be used where AC power is not available.
- Also the heat from the oven can stress fiber if the temperature is not being controlled.
Why would you choose one curing method over another? This refers to your company production requirements such as process speeds, stable production and curing homogeneity.
Understanding the curing process is a concern in order to optimize the conditions where optical fibers are manufactured to improve product reliability, which is because it is extremely important to assure the quality of the finished product since it will affect your market.
Our company, Beyondtech, uses the heat curing method in specialized ovens that works with a stable temperature of 100°C for 45 minutes that will guarantee a finished product with high quality and performance using the “Epo-Tek 353ND”, a two component Epoxy that is well known for its performance and reliability.
In order to get the best for your company, you can contact our customer service team in Beyondtech for any inquiry you may have.
Customer Service: +1.844.283.5266
Technical Support: +1.305.897.3507